Applications
Electronic Components
Solution for electronic components
The demand for electronic components is on the rise, driven by the accelerating electrification in automotive applications and the expanding need for telecommunications equipment amid the COVID-19 pandemic and the spread of 5G technology.
These dynamic market needs necessitate frequent updates in the function, performance, and specifications of electronic components.
As a result, the electronic components industry must continually adapt and innovate to stay aligned with these evolving requirements.
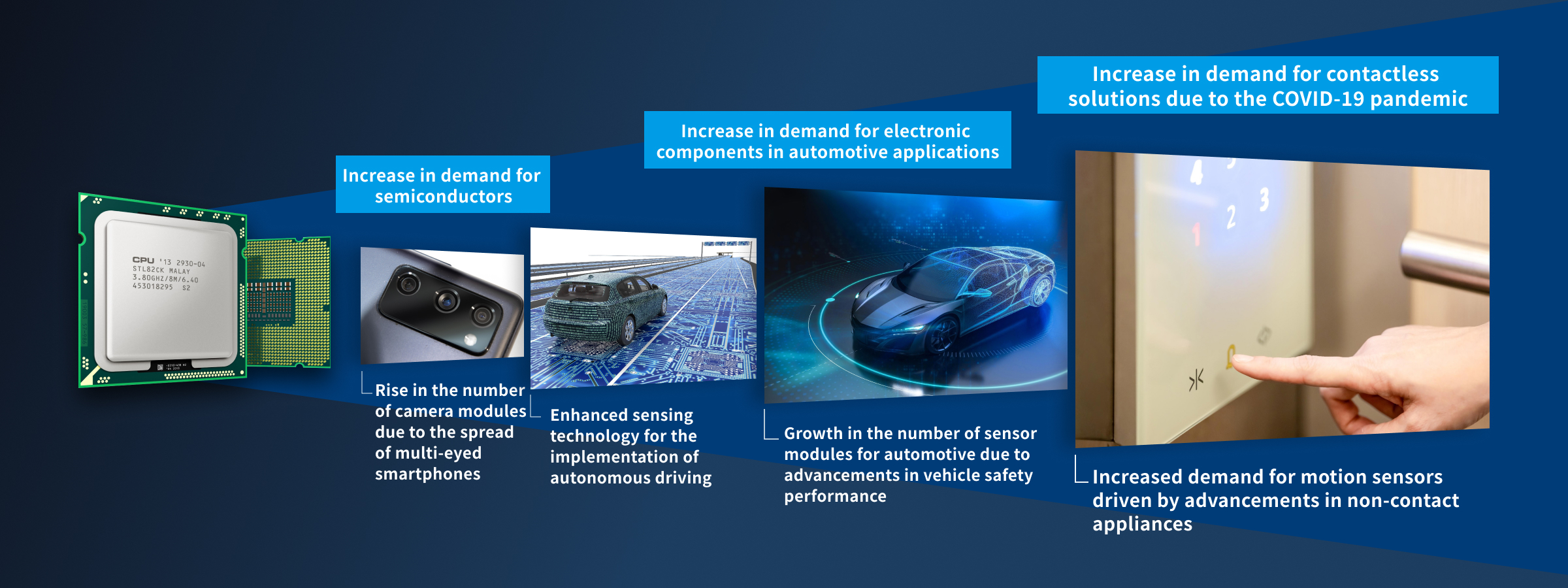
Trends in various modules
-
Camera modules
In the consumer electronics sector, Camera modules are essential components in various smart devices and drones.
In the automotive sector, its demand is increasing for new applications, such as rear and forward cameras for accident prevention
and surround view systems including cabin monitoring, and electronic mirrors. -
Automotive modules
The number of installed automotive image sensors is increasing for applications such as surround view, electronic mirrors, and security systems.
Furthermore, there is a wide range of applications for automotive modules, such as various sensor modules required for safety functions and communication modules connecting with others. -
Telecommunication modules
Demand for remote conference tools are increasing, driven by the need to streamline operations due to work-style changes during the COVID-19 pandemic.
This includes multi-device support, teleworking, and remote working solutions. -
Non-contact temperature sensor modules
Demand for non-contact temperature sensors is projected to grow, prompted by the implementation of thermal cameras at facility entrances in response to the COVID-19 pandemic.
Performance requirements for electronic component mounting
-
High Cleaning Performance
In certain instances, cleaning flux residues is essential for enhancing reliability.
Moreover, the increasing miniaturization and density of components require higher flux residue cleanability in micro patterns. -
For Micro-pattern Applications
To address space constraints, modules are becoming smaller and lighter. This necessitates the use of solder paste with fine particles to apply micro-patterns on substrates
-
Compatibility with various mounting methods
Depending on the module product, mounting methods may vary from standard flat mounting and include techniques such as 3D mounting, laser heating, and other specialized approaches.
-
Extended product life
With the shift towards EVs, the number of automotive substrates being installed is rising. The primary challenge is to improve the reliability and longevity of products exposed to harsh environments.
-
Prevention of solder re-melting
In certain cases, multiple reflow processes are conducted before the various components are modularized.
To prevent solder joints from re-melting during multiple reflow operations, it is important to use solder paste with different melting points. -
Ensuring high surface-mount quality
The diverse range of components incorporated in a module necessitates consistently high surface-mount quality across various base materials and surface finishes.
Related Products
KOKI is continuously developing a wide range of products utilizing advanced alloy and flux technologies to provide optimal solutions for Surface Mount production with electronic components and modules.
The following technologies are proposed as solutions for high surface-mount quality.
Cleaning
Combines cleanability and electrical reliability, making it suitable for both no-clean and clean processes
Fine-Pitch
Enabling reliable and high-quality mounting for fine, ultra-fine components, including 0201, 03015, and 0402 metric chips.
Applicable for transfer method
Applicable solder paste supply using the transfer method for package stacking (PoP method)
Non-contact dispensing
Enabling 3D mounting with non-contact solder supply methods
as represented by jet dispensing
Non-contact heating
Realizing soldering by non-contact heating method (laser heating)
High Reliability
High Reliability alloy with significantly enhanced resistance to thermal cycles compared to the conventional SAC305 alloy
High Temperature
Preventing solder re-melting through multiple reflow operations with higher melting point than SAC305
Multi-function feature
Realizing multi-function features in one flux formulation
(Powerful wetting・Low voiding・Low flux splattering・ICT applicable ・ Halogen-free)
-
指定された投稿は見つかりませんでした。
Other Applications
Contact Us Inquiry
For any requests for estimates, product information, technical questions, etc. please reach out to us.