Applications
Mobile・Smart Devices
Production challenges in mobile, smart devices
The transition of communications standard from 4G to 5G is anticipated to increase the number of components and require larger internal installation area to reduce the overall size of the devices while enhancing its multifunctionality.
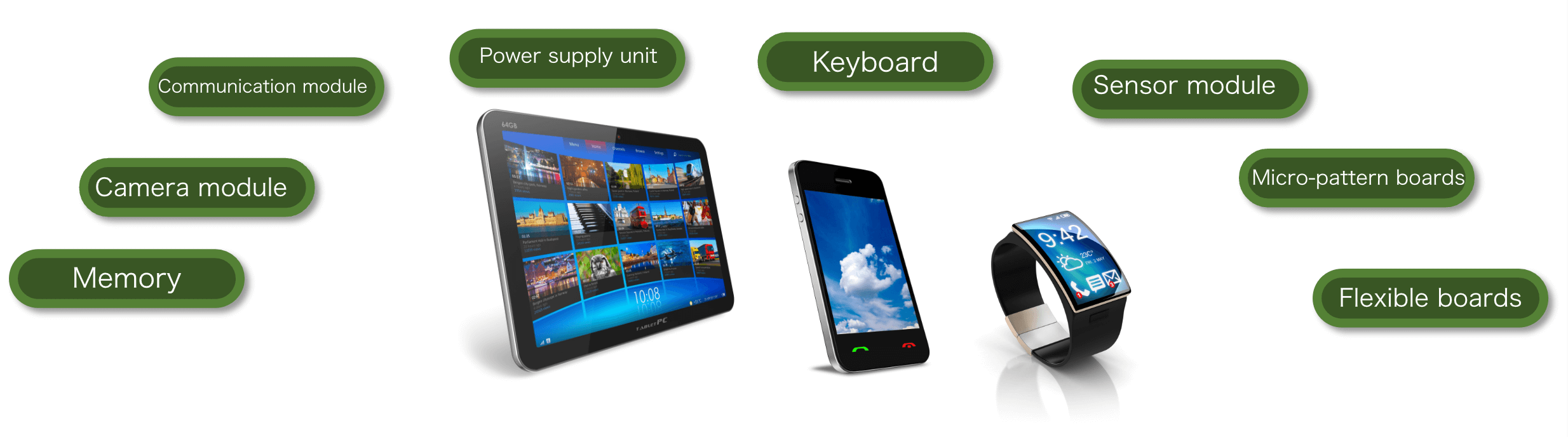
-
Miniaturisation of mounted components
Ceramic capacitors are progressively miniaturizing, now reaching sizes as small as 0201 metric.
By improving functionality of devices hereafter, the demand for these fine components will continue to grow. -
Material cost reduction
In the mobile industry, reducing material costs is crucial due to the intense price competition.
One effective solution is to decrease the content of precious metals like silver, which significantly impacts material costs. -
Securing mounting space for components
As electronic devices are becoming smaller and high-density mounting in accordance with improvement of functionality,
component stacking becomes a crucial method for limited board space.
Package stacking (PoP method) offers a higher degree of flexibility in addition to a chip component stacking. -
Weight-saving
Thin and lightweight substrates like flexible and PET materials are becoming essential for product miniaturization.
Applying low-temperature soldering on PET substrates not only reduces costs but also CO2 emissions, contributing to carbon neutrality. -
Complexity of component mounting points
Non-contact supply by jet dispenser
As mobile/smart devices evolve and feature increasingly complex component mounting points,3D mounting solutions are becoming more common. For these advanced designs,
where traditional printing methods are inadequate, non-contact solder paste application is essential. -
Compatible with a wide range of mounting components
The functionalization of mobile devices has led to a greater variety of component types and electrode materials, including mounting both large and small components on the same substrate.
This diversity has increased the range of mounting characteristics required.
Related Products
KOKI is continuously developing a wide range of products utilizing advanced alloy and flux technologies to provide optimal solutions for Surface Mount production in the mobile industry.
The following technologies are proposed as solutions for the mobile industry.
Fine-Pitch
Enabling reliable and high-quality mounting for fine, ultra-fine components,
including 0201, 03015, and 0402 metric chips.
Low Cost
Achieving cost reductions by lowering silver content and incorporating
strengthening elements to enhance durability beyond that of SAC305 alloy
Applicable for transfer method
Applicable solder paste supply using the transfer method for package stacking (PoP method)
Low Temperature
The use of low temperature alloys enhances compatibility with Flexible / PET substrates,
while reducing costs and improving environmental sustainability.
Non-contact dispensing
Enabling 3D mounting with non-contact solder supply methods
as represented by jet dispensing
Multi-function feature
Realizing multi-function features in one flux formulation
(Powerful wetting・Low voiding・Low flux splattering・ICT applicable ・ Halogen-free)
-
指定された投稿は見つかりませんでした。
Clack-free flux residue
The flexibility of the flux residue helps prevent cracking due to bending in flexible substrates.
Other Applications
Contact Us Inquiry
For any requests for estimates, product information, technical questions, etc. please reach out to us.